Quick Summary
Young’s modulus is an important material property in engineering:
- It is a measure of the stiffness of a material (i.e. a measure of how much a material will deform when acted on by a force).
- Metals and ceramic materials tend to have high Young’s modulus values, whereas polymers have much lower values (they deform more for the same applied load)
- In the elastic region of the stress-strain curve the slope of the curve is equal to Young’s modulus. Young’s modulus can be calculated as an applied stress divided by the resulting strain – this equation is called Hooke’s Law.
Young’s modulus is a really important material property that appears all the time in engineering and physics. It’s used for everything from calculating when a column will buckle to determining how much a beam will deflect when forces are applied to it. So let’s learn more about it!
What is Young’s Modulus?
Young’s modulus, also called the elastic modulus, is a material property that describes how much a material will deform when a load is applied to it. It is essentially a measure of how stiff a material is.
The easiest way to visualise Young’s modulus is on a stress-strain curve, shown in the image below, that can be obtained by performing a tensile test on a sample. The curve can be divided into two regions, an elastic region and a plastic region. If the applied stress is low and we remain in the elastic region – the original dimensions of the material will be completely recovered when the applied load is removed. For larger stresses that take us into the plastic region, permanent plastic deformation will remain after the applied load is removed.
The stress-strain curve is a straight line in the elastic region for most materials. The slope of this curve is equal to Young’s modulus, which is denoted using the letter $E$. Young’s modulus describes the relationship between stress and strain in the elastic region. The higher the Young’s modulus of a material, the smaller the elastic deformations (strain) will be for a given applied load (stress).
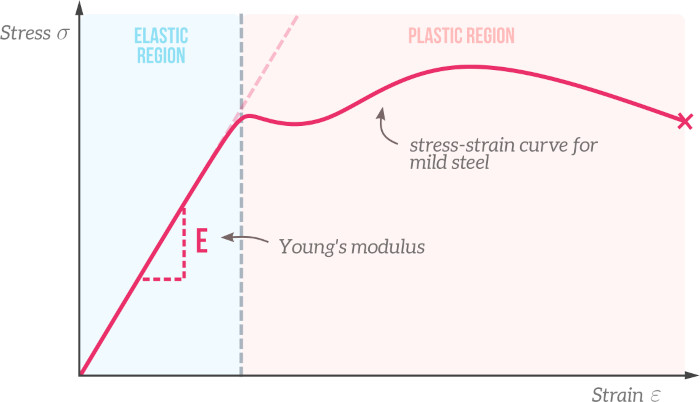
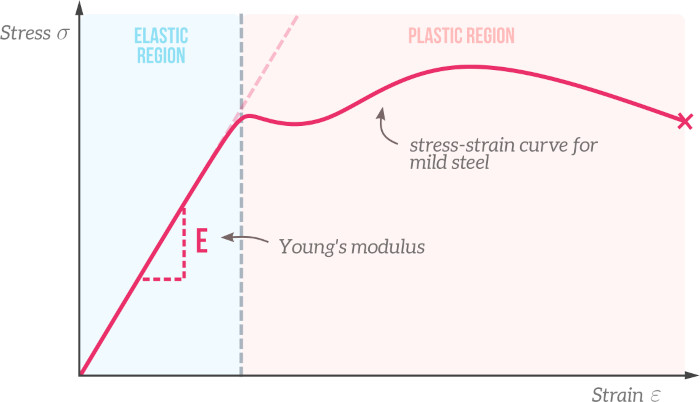
Hooke’s law gives us the relationship between stress and strain in the linear elastic region of the stress-strain curve.
Since strain is dimensionless, Young’s modulus has the same units as stress. Steel has a high Young’s modulus of around 200 GPa, whereas Polystyrene has a low Young’s modulus of around 3 GPa.
Check out the video below if you want to watch an animated summary of all of this information about Young’s modulus. If not, just keep reading!
Applications of Young’s Modulus
Young’s modulus is very important when it comes to engineering, because so often engineering design and analysis involves determining how much something will deform. A high Young’s modulus value is good if you want deformations to be very small – you wouldn’t want a bridge to deform much when a car passes over it, for example, so it would make sense to construct the bridge from materials with a high Young’s modulus.
Because it defines the relationship between stress and strain, Young’s modulus appears in all kinds of different equations that are commonly used in mechancal and civil engineering. Here are a few examples:
How to Determine Young’s Modulus
If you have data from tensile tests performed for a particular material, it’s easy to figure out what the Young’s modulus for that material is. All you have to do is take two points in the linear elastic part of the stress-strain curve, and use those points to measure the slope of the curve. This is illustrated in the figure below.
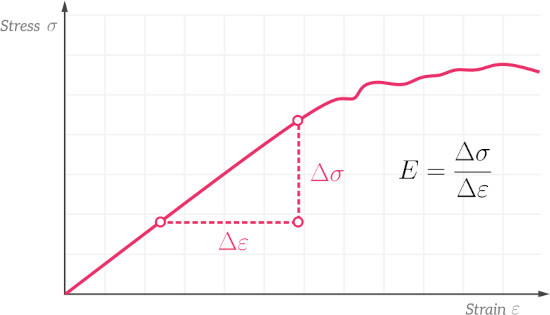
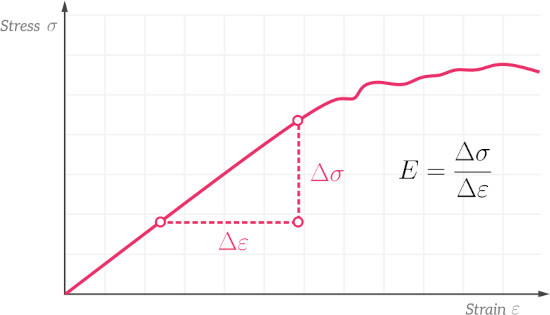
Young’s Modulus Values for Different Materials
The image below shows stress-strain curves for a few different materials. Material 1 has the steepest slope in the elastic region, which means that it has the largest Young’s modulus – you will need to apply a much larger force to deform Material 1 than you would to deform Materials 2 or 3 by the same amount. The stress-strain curve for Material 1 is typical of diamond, for example, whereas Material 2 is more like steel, and Material 3 is typical of a material like rubber.
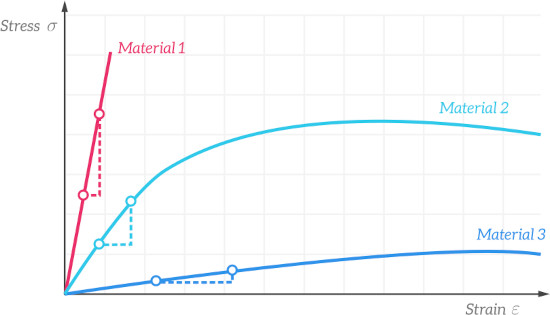
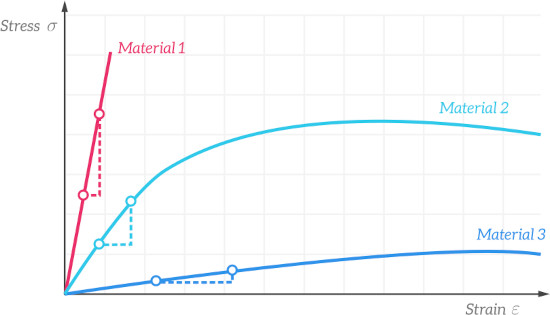
The table below shows typical Young’s modulus values for a few different materials. Ceramics and metals generally tend to have quite high Young’s modulus values, meaning that they are quite stiff. Polymers on the other hand have much lower values.
Material | Young’s Modulus [GPa] |
---|---|
Rubber | 0.1 |
Polystyrene | 3 |
Aluminium Alloy | 69 |
Titanium | 120 |
Copper | 130 |
Carbon Steel | 207 |
Tungsten Carbide | 600 |
Diamond | 1200 |
Understanding Young’s Modulus Using the Ball-and-Spring Model
The Young’s modulus of a material is closely related to the strength of the bonds between its atoms. We can think of these interatomic bonds as small springs connecting adjacent atoms, represented by balls.
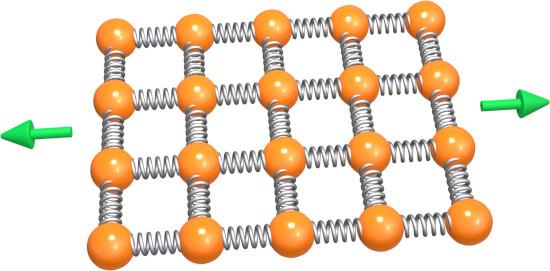
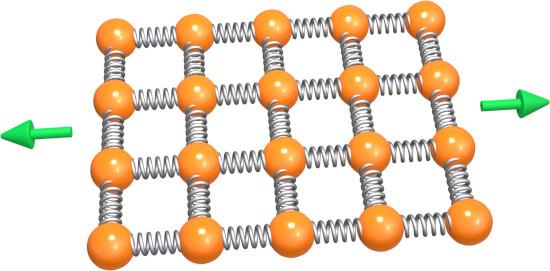
When a force is applied to the material, deformation of the material is resisted by the stiffness of the interatomic bonds. Young’s modulus is a measure of how strong the interatomic bonds are, or in other words it is a measure of how stiff the springs between the atoms are. When the force is removed the atoms return to their initial position – this is elastic deformation.
The mechanism behind plastic deformation is very different, because it involves the breaking of bonds and the re-arrangement of the position of the atoms.
- caused by the stretching of the bonds between atoms
- deformation is reversed when the load is removed
- caused by interatomic bonds breaking at dislocations
- deformation is permanent and remains after the load is removed.